Equipped with 3 - 8 electric CNC axes, multiple tube bending stacks, and the unique technology, this line of LYM tube benders can offer one of the highest performance solutions available in the market.
Tube Bending + Cutting Cell(Optional)
It can be integrated with Automatic Loaders (AF, AFM, Robots) and Automatic Unloaders (AUL, Robots) for full automation. This tube bender series can offer one of highest performance solutions available in the market.
The LYM System
•Allows for automation of bending and cutting processes in one machine, from a single tube
• This system creates minimum cutting deformation, enabling the finished part to pass to the next process without having to calibrate or deburr it
• Allows up to 18 sets bends((PLC type) on the same pipe,or 33 sets bends( Industrial computer type)on the same pipe,maximizing utilization of the complete tube.
• Ultra-large CPU that can hold the edition of 400 groups of archives is applied. If it is not sufficient, transmission software can be purchased and installed for the computer. The archives can be stored in hard disk to expand the number of edit groups infinitely. (Optional)
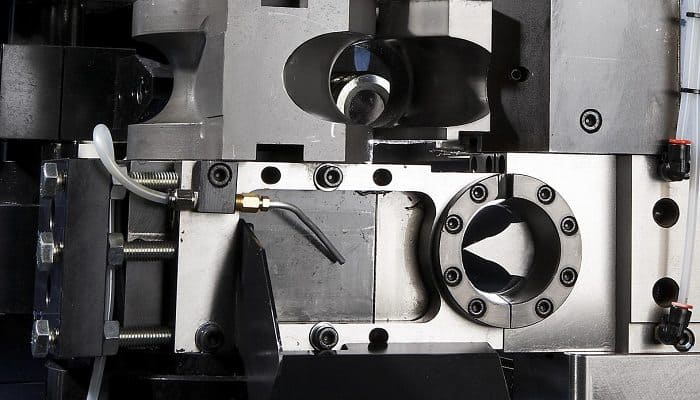
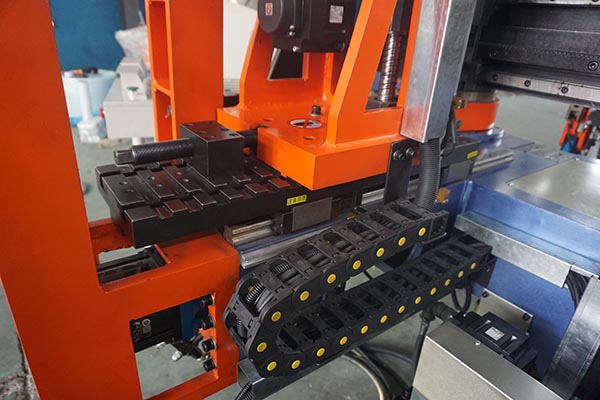
Advanced Technology
•Built-in gearbox with direct connection to electric servo.
•Highest transmission performance (90%+ efficiency).
•High bending accuracy (+/- 0.05° ~ +/-0.1°)
•Maximum Working Area and Minimal Interference.
•Heat exchanger is provided for the electric control system for automatic heat dissipation. If required, NC air conditioner can be purchased to ensure service life of electric control system. (Optional)
•The machine is provided with automatic oil injection system to reduce friction of elbow and ensure quality of elbow. (Optional).
LYM Controls, Tube Bender Software and Operation Interface
• Automatic springback compensation Recapturing function for short lengths XYZ and YBC coordinates conversion
• 3D display of bending parts(Optional) Mirroring and image reversal of parts
• Windows platform
• Self-diagnostics + Error messages display
• Each bends can set compensation value, speed and demould clearance according to different materials
• For same tube, each elbow can have 5 action sequences and 10 sections of speed independently for operation of operators. Besides, the work efficiency can be improved and tube interference point can be reduced.
• Chinese and English on the touch screen can be switched and the products can also be ordered according to requirements if it is another language on the screen. (Optional)
• The feed position of feed trolley, the interference position of safety device and digital module and interference position of guide mould can be fine adjusted manually and memorized automatically to eliminate the error of manual measurement and losses caused by machine collision.
• Action segments can be selected during actual bending to observe interference points and modification work and improve efficiency.
• After the completion of data editing, the data will be protected by password to prevent unapproved alteration of the data. (Optional)
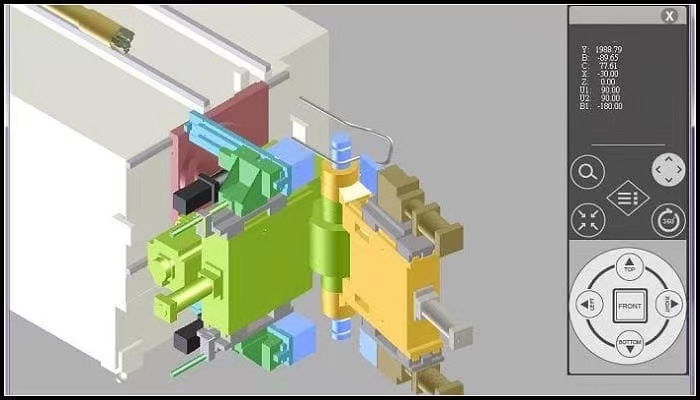
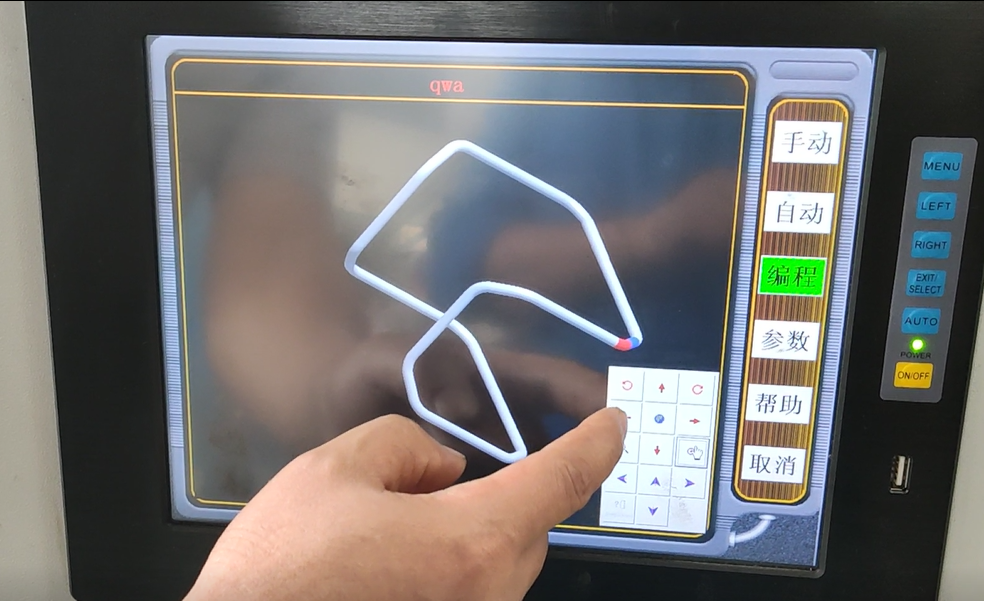
3D Display and Rotation of Parts(Optional)
• XYZ and YBC coordinates conversion
• Mirroring and image reversal of parts